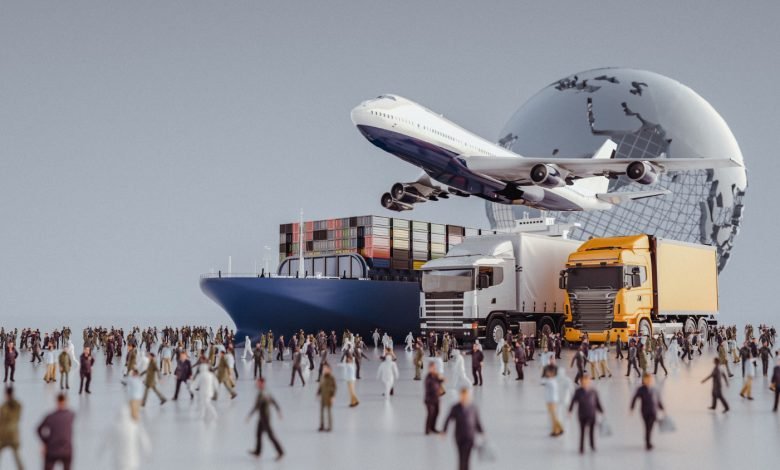
Speeding Up Your Warehouse and Delivery Processes
Steps you can take to help speed up your warehouse delivery process
The faster you ship, the better customer satisfaction will be. And the happier your customers will be with your service in the long run. This is the same in any industry. To ensure your warehouse shipments remain on schedule, there are a number of steps you can take to help speed up your delivery process.
The Future of Warehouse Management
Even today it’s common for workers to move around the production floor taking inventory with pencils and clipboards. But, that’s not indicative of the future. The future of warehouse management is the automation of tedious procedures with real-time access to vital data.
“Warehouses will be constructed on current effective process-driven technology like extensive supply chain automation, hyper-effective robotic technologies, and yes, plenty of drones,” 6 River Systems forecasts.
Newly developed artificial intelligence-enabled ERP software combined with the industrial internet of things (IIoT) sensors will lead the push.
Inventory turnover
Automating these processes will result in faster shipments, reducing your inventory turnover time. In other words, instead of sitting on unsold merchandise for weeks or months at a time, you’ll be able to move inventory through your warehouse as quickly as possible.
The faster you turn over your products, the more control you have over shipping times. Start by taking a hard look at which products are moving slowly; consider investing in new ways to bring those items to market (like an e-commerce store). Then put some controls in place. Create a schedule for restocking slow-moving products and keep regular tabs so they don’t run low before it’s time for an order. If a customer orders one of these slow movers just as it looks like you’re about to sell out, you can be ready with an automatic or manual replenishment request. Finally, make sure everyone is aware of the delivery deadlines—if something isn’t going out today because of a holiday weekend or staffing issues, communicate that change upfront. Customers will understand if you tell them why shipments are being delayed; keeping them waiting without explanation only leads to frustration and churn.
Update your operations
Core operations are a vital part of your business’s success, and if they aren’t updated periodically, you could be slowing down your supply chain considerably. On top of optimizing logistics and improving supplier relations, there are a number of warehouse management technologies that can help. There are a number of solutions that provide real-time information on what needs to be done at each step in shipping—so it’s easy for you and your team members on the ground level to coordinate.
Deploy RFID technology
Radio-frequency identification (RFID) is a great way to track goods and speed up your warehouse shipment. RFID tags are easily attached to goods and provide real-time updates about their location, temperature, physical position, and other data points.
This can be incredibly useful if you’re moving items through a large number of warehouses or want more detailed info on shipments that have been sitting in storage for an extended period of time. Radio-frequency systems will also help you improve your supply chain logistics because they are so precise;
Streamline shipping processes
In supply chain and logistics, speed is of utmost importance. Once an order has been received, it’s up to you to get that product in transit as quickly as possible. If a customer receives their product faster than anticipated—and especially if they receive it sooner than projected—they’re much more likely to become repeat customers.
The best way to streamline your shipping processes is by continually optimizing and reevaluating those systems. So, every aspect of shipping can be streamlined: from receiving incoming shipments, through assembling orders, through printing labels and verifying the accuracy, right on down to packing items in boxes and sending them off via carrier service.
Warehouse Management Software
The key to success is a good warehouse management software (WMS) system. This helps you automate tasks, reduce mistakes and make sure that nothing falls through the cracks. A comprehensive WMS will also let you track shipments from initial pick-up to final delivery. And speeding up your shipping and cutting costs every step of the way. You’ll know exactly where your packages are at all times, even if they’re in transit across different carriers. Because WMS keeps such detailed records, it can significantly speed up and streamline all aspects of your supply chain. From ordering inventory to processing returns—and reducing logistic errors by 100 percent or more.
It seems like everyone is trying to build their own API these days; meanwhile, many companies are still struggling with basic foundational needs—like logistics tracking. However, there’s no need to reinvent a process that’s already been perfected by so many others in other fields. Use a good WMS and save yourself some time and money along every step of your warehouse shipping process.
Final Thoughts
For logistics managers, it can be difficult to keep operations running smoothly. Especially, when it comes to your warehouse and supply chain. Despite how simple warehouse shipment can seem at first glance, it can be a fairly complicated process that involves several moving parts. To that end, it’s important you pay close attention to all elements of operation flow, including critical elements such as processing and picking orders. For this, you need employees who can handle tasks quickly and efficiently, and a powerful system to support them. Is your warehouse ready?
I’ve been taking [url=https://www.cornbreadhemp.com/products/cbd-sleep-gummies ]gummies for sleep[/url] concerning a while at once, and they’ve creditably been a game-changer against stress and sleep. The excellent part? No grogginess in the morning unbiased a balmy, pacific impression rather than bed. Supplementary, they stylishness extraordinary, unlike some other supplements I’ve tried. I was skeptical at first, but after day by day using them, I can indubitably bruit about they help with unwinding after a long day. If you’re looking on a reasonable personality to chill without any strange side effects, CBD gummies are significance trying. Honest make steady you fathom a eminence stamp with third-party testing!