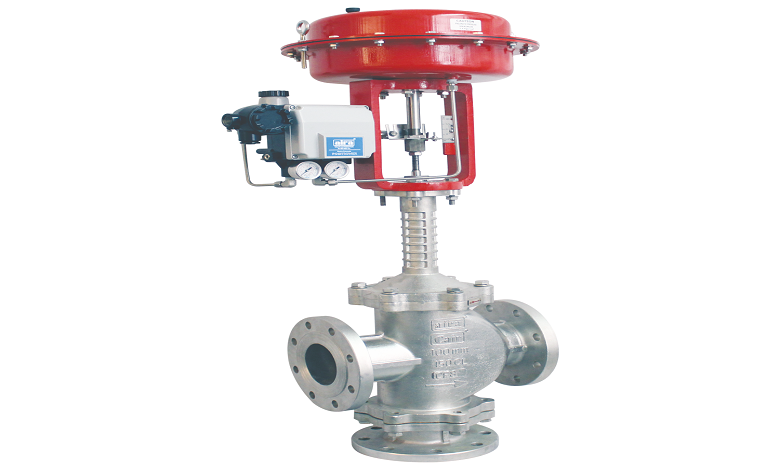
Installation and use of pneumatic control valves are highly demanded today, not only in industries but in everyday applications as well. What do you know about this valve so far? If not, let’s take a look at its structure and operating principle.
Principles of Control Valve:
In an air pressure system, pneumatic globe control valves control the flow rate and speed precisely. Using feedback and control signals, pneumatic actuators precisely open and close these valves.
Structure of Control Valve:
There are two main parts to a globe control valve, the pneumatic actuator, and the globe valve. Other equipment includes pneumatic valve positioners and pneumatic solenoids…
Body of a globe valve
During the opening of the globe valve, the body is directly in contact with the main pressurized fluid as well as storing all the information about the valve. Generally, the valve body consists of a pair of ports oriented directly opposite each other or anywhere on the body or oriented at 90° angles (angle globe valve). Nowadays powder coated instruments are in demand. The valve body also available in powder coated body.
The most common use of globe valves is to handle corrosive, high temperature, and high pressure viscous fluids. In a horizontal pipe, there will be residual liquid in the valve body, which will cause clogs or corrosion if left unused for a long time. In this case, we can use oblique or angle globe valves. Usually, valve bodies are made of heat- and force-resistant alloys such as cast iron, stainless steel, steel…
Pneumatic Actuator
Globe valves typically have two types of pneumatic actuators: pistons and diaphragms. Globe valves use sliding motion as opposed to ball valves and butterfly valves, which use rotary motion.
Piston-type Pneumatic Actuator
A piston and barrel move within a structure that is similar to a pneumatic cylinder. A globe control valve shaft is connected to a piston. When compressed air pulls the piston up, the valve opens, when compressed air pushes it down, the valve closes.
Actuators with pistons are available in two configurations: single and double acting.
In double acting types, compressed air is used to push the piston both during opening and closing. An air-powered double-acting actuator is entirely dependent on the pressure of compressed air to open or close.
A single-acting form only relies on pneumatic pressure to open or close the valve once, then relies on additional spring force to complete the other cycle. Single-acting actuators have one or more springs to perform opening or closing the valve.
The piston actuator typically has a longer stroke and greater thrust than a diaphragm actuator.
Pneumatic Diaphragm Actuator
It is a single acting actuator. There are two main parts: the diaphragm and the spring. The membrane moves with its elastic force after the spring is firmly pressed. The low cost, simple structure, easy installation, and ease of operation of this type of device make it popular for controlling globe valves.
Pneumatic Valve Positioner
Positioners are what do they do? (Pneumatic valve positioner): works on the principle of force balance to control valve disc rotation according to a pneumatic command. This positioner determines the precise angle for valve opening/closing and provides air to the actuator. Therefore, the positioning device ensures accurate and stable pneumatic valve operation. An additional device, usually attached to the actuator shaft, monitors the valve position and the position of the valve disc.
Structure and operating principle:
Essentially, pneumatic globe control valves have two main opening and closing cycles, as well as smaller cycles for damper valves.
Valve closing cycle (fully closed)
In an actuator driven by a solenoid valve, pneumatic pressure pushes the piston or diaphragm against the elastic force of the spring, which causes the piston or diaphragm to compress along the valve shaft until it reaches its limit and the valve closes.
Valve opening cycle (fully open)
By switching to an open state, the solenoid valve stops providing compressed air to the system and the compressed air exits the system. In a fully open valve, the spring’s elastic force pushes the piston or diaphragm up, pulling the shaft to the valve stem.
Regulating cycle (partially open/closed)
The close and open cycles are different by these small cycles. During this cycle, the compressed air pressure only pushes the piston or diaphragm a short distance than the full valve opening / closing stroke, the purpose being to partially open / close the valve disc for flow control and regulation.
Pros and cons
As with all pneumatically controlled globe valves, they are intrinsically safe, without risk of fire and explosion, and they have the capacity to close with significant force against large pressure differentials.
Advantages
- Good at switching off
- Good flow regulation capability
- In comparison with gate valves, the valve opening and closing strokes are shorter
- Easy production and maintenance thanks to a simple structure
- The valve are use as a check valve if the disc is not attach to the valve shaft
Defect
- There is a substantial pressure drop in the fluid passing through
- Due to the fluid pressure affecting the disc when the valve close with high-pressure systems and it is extremely difficult to close the valve
- Valves are not suitable for fluids containing granular materials or low viscosity
- Costlier than similar-sized valves
Application
Among the fluids that are suitable for pneumatically operated globe valves, water, hot steam, compressed air, gases, and other fluids with corrosive properties are among the most common.
Globe valves are typically use for the following applications:
- Water cooling system with a regulated flow to save money
- A system that regulates oil flow is of great importance to fuel oil systems.
- A system for taking care of water, chemicals, condensate gases, and drainage
- In the case of boiler vents, main vents, and heat pipes
- Lubricated turbines
You can contact us at Aira Euro Automation. if you still have questions about selecting the right pneumatic valve after reviewing this information. As well as distributing genuine valves, we also offer free consultation, enthusiastic customer support to help you find the suitable valve that best fits your needs, at an affordable price.